Back in 2021, when Habitat for Humanity and 3D-printing company Alquist debuted their first 3D-printed home, it seemed like the beginning of a boom.
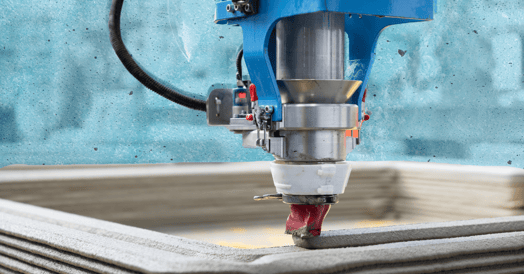
Three years later, 3D printing hasn’t yet turned the construction industry on its head, but that doesn’t mean it’s not trying.
Slow going, but going nonetheless
The 3D-printing construction market was worth $3.4B in 2022 and, despite a slow start, is still projected to hit ~$519B by 2032.
If you need more concrete evidence than that, just look at what 3D-printing firm Icon is up to in the Texas desert:
- The world’s first 3D-printed hotel, El Cosmico, will house camping areas, vacation homes, residences (starting at $2.3m), and amenities on 60+ acres outside of Marfa.
- The curved, dome-topped buildings will be made with Lavacrete, a proprietary cement-like mixture poured with Icon’s Vulcan 3D-printing system.
The process isn’t completely devoid of humans: Once the basic structures are complete, contractors will add finishing touches like roofs, electric, and windows.
Building anticipation
While a 3D-printed desert city is difficult to top, there are other recent projects of note:
- Wolf Ranch, another Icon project, is a community of 100 3D-printed houses ~30 miles outside of Austin. The prices range from ~$450k to $600k, and 25+ have already been sold.
- In 2023, Detroit’s first 3D-printed home hit the market for $224.5k.
While 3D-printing might be moving slower than we thought, it still has its perks — it can accelerate construction timelines, reduce material waste, allow for more customization, and reduce human error and on-the-job injuries.