In this economy, I’d live in anything that had an in-unit washer and dryer.
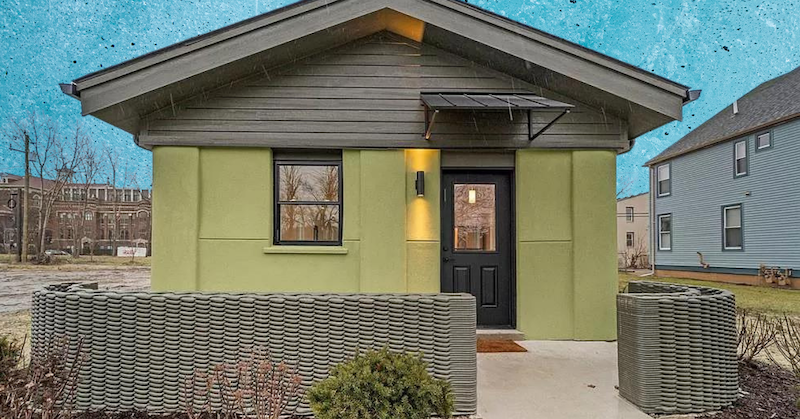
But that question is more than hypothetical for whoever moves into a 988-square-foot 3D-printed home in Detroit.
They can print houses now?
Sure can. Citizen Robotics, a nonprofit seeking to make housing affordable through robotic construction, printed the pieces at a facility in southwest Detroit, then assembled the home on site.
What that means is that a robotic arm — typically used in auto manufacturing, the industry that has long defined Detroit — layered a cement material to build walls, per The Detroit Free Press. (Watch a demo here.)
It’s a cheaper process that requires less time and fewer people than pouring concrete into a form. Citizen Robotics said it’s also strong and affordable, and will likely reduce heating and cooling costs by ~$120 per month. Those costs could be fully covered if the owner installs solar panels.
But…
… it’ll still cost you $224.5k to call this two-bed, one-bath house yours.
That might seem like a steal in NYC or LA, but it’s very high for Detroit, where most homes sell for under $100k. Unsurprisingly, there’s been no sale, per Business Insider.
The problem, according to Bryan Cook, the architect of the home, is the development process. For 3D-printed homes to actually be affordable, they’d need to be constructed at scale and not as one-offs.
- In Georgetown, Texas, there’s a community of 100 3D-printed homes selling at $475k-$599k each. Georgetown’s median home price is $460k.
There’d also need to be coding changes in some areas, including in Michigan where a requirement to reinforce walls with concrete columns increased costs.
BTW: NASA intends to 3D-print homes on the moon.